Siding Installation Services In New Zealand
Siding Installation Services In New Zealand: Transforming Kiwi homes, one perfectly installed panel at a time. From the rugged beauty of the South Island to the vibrant cities of the North, the choice of exterior siding significantly impacts a home’s aesthetic appeal and longevity. This comprehensive guide dives deep into the world of New Zealand siding, exploring everything from material selection and installation processes to cost considerations and regulatory compliance.
Whether you’re a homeowner embarking on a renovation or a seasoned professional seeking to refine your skills, this resource offers invaluable insights into the thriving New Zealand siding market.
We’ll unpack the nuances of different siding materials—vinyl, fiber cement, weatherboard, and more—analyzing their suitability for diverse New Zealand climates and building codes. We’ll then guide you through the intricacies of professional siding installation, covering essential tools, safety protocols, and troubleshooting common challenges. Finally, we’ll empower you with the knowledge to select a reputable installer, negotiate contracts effectively, and maintain your siding for years to come.
Get ready to unlock the secrets to a stunning and durable exterior.
Understanding the New Zealand Siding Market: Siding Installation Services In New Zealand
New Zealand’s diverse climate and architectural styles create a dynamic market for exterior cladding, commonly known as siding. Choosing the right siding material is a significant decision impacting both the aesthetic appeal and longevity of a home. This section delves into the various siding options available, exploring factors influencing material selection across different regions and providing a comparative analysis of cost and lifespan.
Siding Materials in New Zealand Homes
Several siding materials cater to the diverse needs of New Zealand homeowners. Common choices include timber, fiber cement, vinyl, and metal. Timber siding, often cedar or treated pine, offers a classic, natural look, while fiber cement provides durability and fire resistance. Vinyl siding presents a low-maintenance, budget-friendly option, and metal siding, such as aluminum or steel, boasts exceptional longevity and weather resistance.
The selection often depends on factors such as budget, aesthetic preferences, and the specific environmental conditions of the location.
Regional Factors Influencing Siding Material Choice
New Zealand’s varied climate significantly impacts siding material selection. Coastal regions, prone to high winds and salt spray, often benefit from durable materials like fiber cement or metal siding, which can withstand harsh weather conditions. Areas with heavy rainfall might favor materials with excellent water resistance, such as certain types of treated timber or fiber cement. Conversely, drier regions may allow for a wider range of options, including vinyl siding, though consideration should still be given to sun exposure and potential UV degradation.
Building codes also play a role, particularly regarding fire safety and structural integrity in specific zones. For example, areas with a higher risk of bushfires may mandate fire-resistant materials like fiber cement.
Pricing and Lifespan of Siding Options
The cost of siding varies significantly depending on the material, installation complexity, and regional factors. Timber siding, while aesthetically pleasing, generally falls at the higher end of the price spectrum, requiring more maintenance over its lifespan. Vinyl siding offers a more budget-friendly alternative, although its lifespan is typically shorter than that of fiber cement or metal. Fiber cement provides a balance between cost and longevity, while metal siding, while initially expensive, boasts the longest lifespan with minimal maintenance needs.
These variations necessitate careful consideration of long-term costs versus upfront investment. For instance, a homeowner might choose a more expensive but longer-lasting material like fiber cement to avoid frequent replacements and associated labor costs.
Comparative Analysis of Siding Materials
Siding Material | Approximate Cost (per m²) | Lifespan (Years) | Maintenance Requirements |
---|---|---|---|
Timber (Cedar/Treated Pine) | $150 – $300+ | 20-40+ | Regular painting, sealing, and potential repairs |
Fiber Cement | $100 – $200+ | 30-50+ | Minimal; occasional cleaning and potential repainting |
Vinyl | $50 – $150 | 15-30 | Low; occasional cleaning |
Metal (Aluminum/Steel) | $150 – $300+ | 50+ | Very low; occasional cleaning |
Note
Prices are estimates and can vary based on several factors, including supplier, installation costs, and regional differences. Lifespan estimates are based on average conditions and proper installation and maintenance.
Siding Installation Processes
Siding installation in New Zealand, while seemingly straightforward, demands precision and adherence to building codes to ensure longevity and weather resistance. The process varies depending on the siding material chosen – each possessing unique properties impacting installation techniques. Understanding these nuances is crucial for a successful and long-lasting result. This section details the steps involved, necessary tools, safety measures, and common challenges encountered during installation.
Vinyl Siding Installation
Vinyl siding, popular for its affordability and low maintenance, requires a specific approach. Installation begins with preparing the wall surface, ensuring it’s clean, dry, and free from any debris. Next, installers establish a consistent starting point, often using a level to create a straight, plumb line. J-channels are installed at corners and around windows and doors to provide a neat finish and protect the edges of the siding.
Vinyl siding panels are then installed, overlapping each panel slightly and securing them with nails placed in the designated nailing slots. The final step involves trimming excess siding and adding finishing pieces to complete the installation. Proper expansion and contraction space must be maintained to accommodate temperature fluctuations. Ignoring this crucial step can lead to warping and buckling.
When investigating detailed guidance, check out Home Security Automation now.
For instance, a 1/8-inch gap should be left between the siding and any immovable objects.
Fiber Cement Siding Installation
Fiber cement siding offers superior durability and fire resistance compared to vinyl. However, its heavier weight and more complex installation process require additional care. The initial preparation is similar to vinyl installation; however, the panels themselves require more precise cutting and fitting, often using specialized tools. Unlike vinyl, fiber cement siding needs to be fastened securely, often requiring more nails or screws per panel to prevent warping.
Furthermore, proper sealing around windows and doors is critical due to the material’s susceptibility to moisture damage. A meticulous approach, focusing on precise measurements and secure fastening, is essential for a quality fiber cement siding installation. Improper installation can lead to cracking and water infiltration, necessitating costly repairs.
Weatherboard Siding Installation
Weatherboard siding, a traditional New Zealand choice, involves a slightly different process. The installation begins with the careful placement of the bottom weatherboard, ensuring a level and straight line. Subsequent boards are then overlapped, typically with a 50mm overlap, and nailed securely to the wall framing. Each board should be aligned with the previous one, maintaining a consistent gap for expansion and contraction.
The use of appropriate nails and spacing is vital to prevent splitting or damage to the boards. Mitered corners and skillful cutting around windows and doors are hallmarks of professional weatherboard installation. The finish is often enhanced with paint or stain for protection and aesthetic appeal. Inconsistent spacing or improper nailing can compromise the water resistance and structural integrity of the weatherboarding.
Necessary Tools and Equipment
Professional siding installation necessitates a range of specialized tools. This includes measuring tapes, levels, saws (circular saw for fiber cement, hand saw for weatherboard), drills, nail guns, and various types of fasteners. Safety equipment such as safety glasses, gloves, and dust masks are crucial for protecting the installer from potential hazards. Additional tools like a chalk line, utility knife, and caulking gun are also commonly used.
The specific tools required will vary based on the type of siding being installed. For example, fiber cement siding may require a wet saw to prevent dust inhalation.
Safety Precautions
Safety is paramount during siding installation. Installers should always wear appropriate personal protective equipment (PPE), including safety glasses, gloves, and hearing protection. Working at heights requires the use of harnesses and fall protection systems, especially when using ladders or scaffolding. Proper handling and disposal of materials are essential to prevent injury and environmental damage. Furthermore, awareness of overhead power lines and other potential hazards is critical.
A comprehensive site assessment before commencing work is always recommended. Ignoring safety protocols can lead to serious injuries or fatalities.
Common Challenges and Solutions
Several challenges can arise during siding installation.
- Uneven wall surfaces: Solutions include using shims to level the siding or employing furring strips to create a more consistent surface.
- Difficult cuts around windows and doors: Precise measurements and the use of specialized cutting tools are essential to ensure a clean and accurate fit.
- Weather conditions: Installation should be postponed in extreme weather conditions such as high winds or heavy rain.
- Material damage: Careful handling and storage of siding materials can minimize damage during installation.
- Improper fastening: Using the correct fasteners and following manufacturer’s instructions are crucial to prevent damage and ensure longevity.
Finding and Choosing Siding Installers
Choosing the right siding installer is crucial for a successful project. A poorly executed installation can lead to costly repairs, diminished home value, and significant aesthetic issues. Therefore, thorough research and careful selection are paramount for New Zealand homeowners. This section provides guidance on finding reputable and experienced professionals.Finding a qualified and reliable siding installer in New Zealand requires a strategic approach.
This involves going beyond simply searching online directories and actively vetting potential candidates. Remember, the right installer will save you time, money, and potential headaches down the line.
Vetting Potential Siding Installers
Before engaging any installer, verify their credentials. Check for valid licenses and insurance coverage, confirming they are registered and compliant with New Zealand building regulations. This protects you from liability in case of accidents or substandard work. Look for online reviews and testimonials from past clients, focusing on the quality of their workmanship, communication, and adherence to timelines.
A company with a consistently positive reputation speaks volumes about their reliability and professionalism. Furthermore, consider their experience with specific siding materials; a company proficient in installing weatherboard might not possess the same expertise with fiber cement.
Obtaining and Comparing Multiple Quotes
It is vital to obtain at least three quotes from different siding installers. This comparative approach allows you to evaluate pricing, services offered, and overall value. Ensure that each quote is detailed and includes a comprehensive breakdown of materials, labor costs, and any additional charges. Avoid quotes that are vaguely worded or lack sufficient detail; this often indicates a lack of professionalism.
Direct comparison of these quotes, focusing on the total cost and the level of detail provided, is a key step in making an informed decision. For instance, one quote might offer higher-quality materials at a slightly higher cost, while another might offer a lower price but use inferior materials. Careful analysis of these trade-offs is crucial.
Key Questions for Potential Installers
Asking the right questions is key to assessing a potential installer’s suitability. Inquire about their experience with similar projects, the specific siding materials they recommend, and their warranty policies. Understanding their project management approach, including communication protocols and timeline expectations, is crucial. Furthermore, ask about their safety procedures and compliance with building codes. A thorough understanding of their process, including permits and inspections, ensures a smooth and compliant installation.
For example, you might ask about their experience with specific types of weatherboarding commonly used in New Zealand homes, or their process for dealing with unexpected issues during installation.
Sample Siding Installation Contract
A well-drafted contract protects both the homeowner and the installer. Essential clauses include a detailed description of the work to be performed, including materials specifications and quantities; a clear payment schedule with milestones; a defined start and completion date; and a comprehensive warranty covering workmanship and materials. The contract should also include dispute resolution mechanisms and a clear Artikel of responsibilities for permits and inspections.
A sample clause might state: “The installer shall be responsible for obtaining all necessary building permits and ensuring compliance with all relevant New Zealand building codes.” Another clause could specify: “Payment shall be released in three installments: 25% upon commencement, 50% upon completion of framing, and 25% upon final inspection and approval.” This detailed structure prevents misunderstandings and ensures a legally sound agreement.
Legal and Regulatory Aspects
Navigating the legal landscape of siding installation in New Zealand is crucial for both homeowners and contractors. Understanding building codes, obtaining necessary permits, and adhering to regulations ensures a safe, compliant, and legally sound project. Non-compliance can lead to significant penalties, delays, and even structural issues. This section Artikels the key legal considerations to ensure a smooth and successful siding installation.Building codes and regulations in New Zealand are designed to maintain safety and quality standards across all construction projects, including siding installations.
These regulations cover various aspects, from material specifications and installation methods to fire safety and weather resistance. Compliance is non-negotiable and forms the foundation of a successful project.
Relevant Building Codes and Regulations
The primary legislation governing building work in New Zealand is the Building Act 2004 and its associated regulations. Specific requirements related to cladding (which includes siding) are detailed within the New Zealand Building Code (NZBC). The NZBC’s clauses E2 (External Moisture) and F2 (External Hazards) are particularly relevant for siding installations, dictating requirements for weather tightness, durability, and resistance to fire and other external hazards.
Local councils also have their own district plans that may impose additional requirements or restrictions depending on the specific location of the project. For example, some areas might have stricter rules regarding colour schemes or the types of materials permitted. Contractors must be thoroughly familiar with both the national building codes and the local council regulations before commencing any work.
Importance of Obtaining Necessary Permits and Approvals
Before any siding installation commences, obtaining the necessary building permits and approvals from the local council is mandatory. This process ensures that the project adheres to all relevant building codes and regulations. The application typically involves submitting detailed plans and specifications, including material choices, installation methods, and any proposed modifications to the existing structure. Failure to obtain the required permits before starting work can result in stop-work orders, significant fines, and potential legal action.
The council’s approval provides legal protection for both the homeowner and the contractor, ensuring that the work is carried out safely and legally. It also helps avoid costly rework or demolition later on if non-compliance is discovered.
Implications of Non-Compliance with Building Codes, Siding Installation Services In New Zealand
Non-compliance with building codes related to siding installation can have serious consequences. These can include: substantial fines levied by the local council; the issuance of a stop-work order, halting the project until compliance is achieved; legal action from homeowners if defects arise due to non-compliance; and potentially even insurance claims being denied in case of damage resulting from faulty installation.
Furthermore, non-compliant siding can compromise the structural integrity of the building, leading to costly repairs and potential safety hazards. A reputable contractor will always prioritize compliance, understanding the significant implications of non-compliance.
Examples of Common Building Code Violations
Common violations often involve improper installation techniques, leading to inadequate weather protection. For instance, failing to correctly flash around windows and doors can allow water ingress, causing rot and structural damage. Using unsuitable materials that don’t meet the specified fire safety standards is another frequent violation. Similarly, insufficient attention to the detailing of joints and overlaps can lead to leakage and damage.
Another common issue is the failure to provide adequate ventilation behind the siding, which can contribute to moisture buildup and the growth of mold. These examples highlight the importance of meticulous planning and execution, guided by the relevant building codes and the expertise of a qualified installer.
Maintenance and Repair of Siding
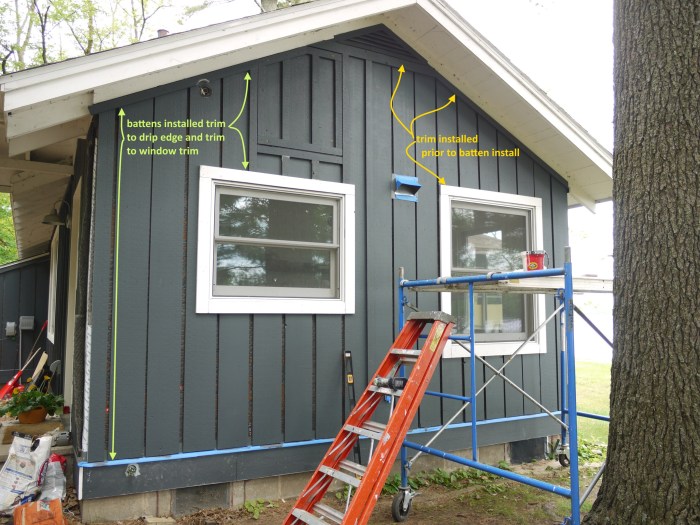
Maintaining your New Zealand home’s siding is crucial for preserving its aesthetic appeal and structural integrity. Regular upkeep not only enhances curb appeal but also prevents costly repairs down the line, extending the lifespan of your investment significantly. Different siding materials require specific care, and understanding these nuances is key to effective maintenance.
Common Siding Issues and Solutions
Various siding materials face unique challenges in the New Zealand climate. For instance, timber siding is susceptible to rot and insect infestation, particularly in damp environments. Regular inspection and prompt treatment with appropriate wood preservatives are essential. Fiber cement siding, while durable, can crack under extreme weather conditions or due to improper installation. Careful inspection for cracks and prompt repairs using patching compounds are necessary.
Vinyl siding, though relatively low-maintenance, can fade in the strong New Zealand sun. Regular cleaning and the use of UV-resistant cleaners can help mitigate this. Metal siding, while robust, can be prone to dents and scratches. Minor dents can often be repaired with a gentle hammer and careful shaping.
Siding Maintenance Schedule
A proactive approach to siding maintenance is paramount. A well-defined schedule tailored to your specific siding type ensures longevity. For timber siding, annual inspections for rot, insect damage, and loose boards are crucial. Cleaning should be done at least twice a year, using a pressure washer on a low setting. For fiber cement, semi-annual inspections for cracks and damage are recommended.
Cleaning can be done using a mild detergent and a soft brush. Vinyl siding typically requires less intensive maintenance; a yearly cleaning with soap and water is usually sufficient. Metal siding benefits from a semi-annual inspection for dents, scratches, and loose fasteners. Cleaning can be achieved using a mild detergent and a soft cloth or sponge.
Identifying and Addressing Water Damage and Insect Infestation
Early detection is critical in mitigating the impact of water damage and insect infestation. Water damage often manifests as discoloration, swelling, or mold growth. Prompt repairs, including replacing damaged boards and addressing underlying moisture issues, are vital to prevent further deterioration. Insect infestation can be identified by the presence of holes, sawdust, or insect activity. Professional pest control may be necessary to effectively eliminate the infestation and prevent recurrence.
Regular inspections and prompt action are key to preventing these problems from escalating into major repairs.
Visual Guide to Common Siding Repairs and Maintenance Tasks
Imagine a series of four close-up images. The first depicts the careful application of wood preservative to a section of weathered timber siding, highlighting the brush strokes and the even saturation of the wood. The second shows a homeowner using a putty knife to smoothly apply a patching compound to a small crack in fiber cement siding, ensuring a seamless finish.
The third illustrates the gentle cleaning of vinyl siding with a soft brush and soapy water, emphasizing the removal of dirt and grime without causing damage. The final image showcases the careful replacement of a dented section of metal siding, with the new panel seamlessly integrated into the existing structure, showcasing precise measurements and tool usage. These images visually represent the key maintenance and repair tasks associated with different siding materials, emphasizing the importance of precision and the use of appropriate tools and materials.
Cost Considerations for Siding Projects
Planning a siding installation in New Zealand requires careful consideration of the associated costs. Understanding the price breakdown will help you budget effectively and avoid unexpected expenses. This section details the various factors influencing the total cost, providing a framework for accurate estimation. Accurate budgeting ensures a smooth project from start to finish.
Calculating Total Project Cost
The total cost of a siding installation project is a sum of several key components: materials, labor, and permits. Let’s break down each element. Material costs vary greatly depending on the chosen siding type, quantity needed, and any additional features like trim or flashing. Labor costs are influenced by the project’s size and complexity, as well as the installer’s experience and hourly rates.
Permitting fees are determined by local council regulations and the scope of the work. A comprehensive breakdown allows for precise financial planning.
Factors Influencing Overall Cost
Several factors significantly impact the final cost. Project size is paramount; larger areas naturally require more materials and labor. The type of siding selected—be it timber, fiber cement, vinyl, or metal—dramatically influences material costs, with some options significantly more expensive than others. Installer experience also plays a crucial role; experienced installers often charge higher rates but may offer superior workmanship and efficiency, potentially offsetting the higher initial cost.
Finally, regional variations in material prices and labor rates can also affect the overall budget.
Cost-Effectiveness of Different Siding Options
Comparing siding options requires considering both initial cost and long-term value. While vinyl siding might offer a lower upfront cost, its shorter lifespan compared to materials like fiber cement or metal may lead to higher replacement costs over the long run. Timber siding, though aesthetically pleasing, often demands more frequent maintenance and repair, influencing its overall cost-effectiveness. A thorough cost-benefit analysis, factoring in lifespan and maintenance requirements, is essential for making an informed decision.
For example, a high-quality fiber cement siding, despite a higher initial investment, might prove more cost-effective in the long run due to its durability and longevity, requiring less frequent maintenance and replacement.
Cost Breakdown Example
The following table illustrates a sample cost breakdown for a medium-sized siding project (approximately 100 square meters) in Auckland, New Zealand. These figures are estimates and may vary based on the factors discussed above.
Item | Unit Cost (NZD) | Total Cost (NZD) |
---|---|---|
Materials (Fiber Cement Siding) | $80/m² | $8000 |
Labor | $50/m² | $5000 |
Permits | $500 (estimated) | $500 |
Total | $13500 |
Note: This is a simplified example. Actual costs may vary significantly depending on specific project requirements and location. Always obtain multiple quotes from reputable installers.
Epilogue
Ultimately, choosing the right siding for your New Zealand home involves careful consideration of various factors—climate, budget, aesthetic preferences, and long-term maintenance. By understanding the diverse options available, navigating the installation process with expertise, and prioritizing adherence to building codes, you can ensure a successful project that enhances your property’s value and curb appeal for years to come. This guide has armed you with the knowledge to make informed decisions, ensuring your siding investment stands the test of time and the elements.
Remember, a well-chosen and expertly installed siding system is not just about aesthetics; it’s about protecting your investment and creating a home that reflects your unique Kiwi style.